Introduction to Cobots
Collaborative robots, often called cobots, represent a groundbreaking advancement in automation technology. Unlike traditional industrial robots that work in isolation, cobots are specifically designed to work alongside humans safely. These innovative machines have rapidly gained popularity across various industries since their introduction nearly two decades ago. Their user-friendly interfaces, flexibility, and cost-effectiveness make them accessible to businesses of all sizes. As automation becomes increasingly crucial for competitiveness, cobots emerge as essential tools for both large enterprises and smaller businesses.
Cobots stand apart from conventional robots through their emphasis on human-robot collaboration rather than replacement. This fundamental shift in approach has opened new possibilities for workplace efficiency and safety. Moreover, cobots help businesses adapt to changing market demands with unprecedented agility and responsiveness.

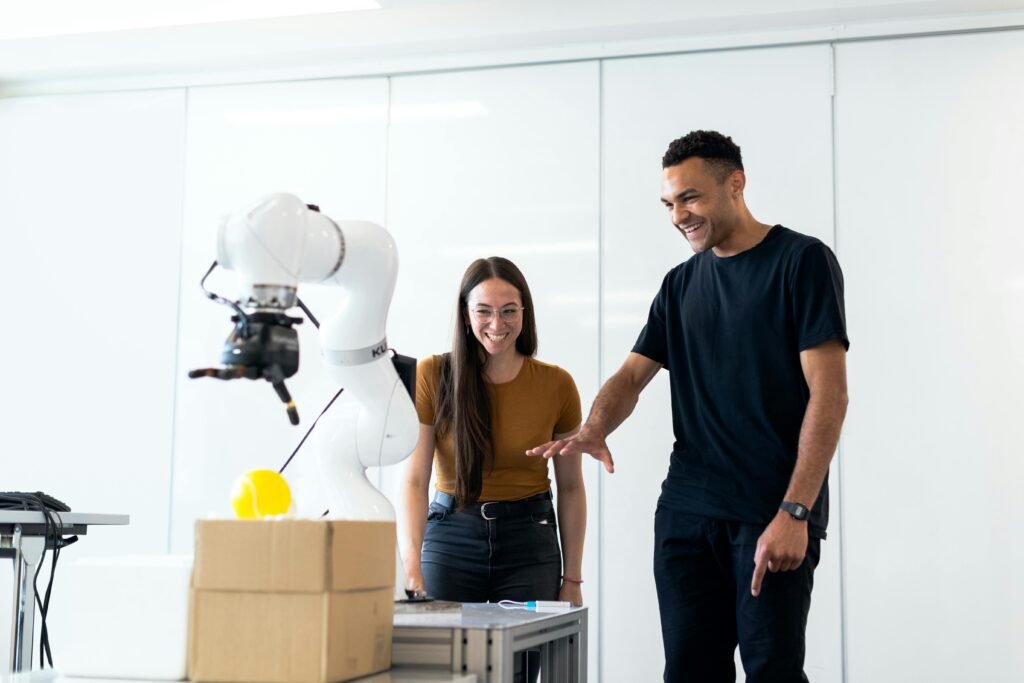
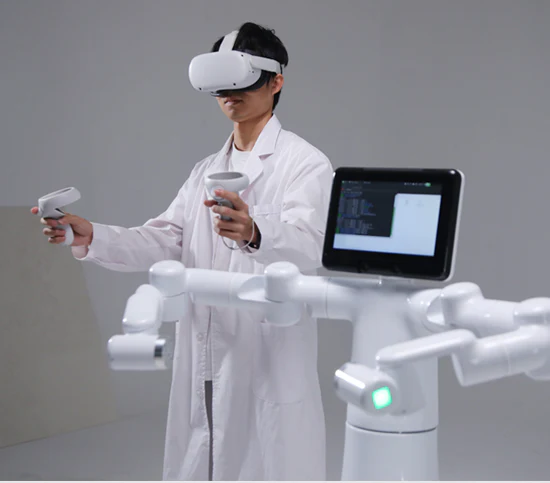
What Makes Cobots Different?
The distinction between cobots and traditional industrial robots lies in their core design philosophy. Traditional robots typically operate in caged environments, separated from human workers for safety reasons. Cobots, however, incorporate advanced safety features that enable them to work directly alongside people. This collaborative approach combines human creativity and problem-solving with robotic precision and endurance.
Further setting cobots apart is their intuitive programming interface. Many models can be trained through simple hand-guidance, dramatically reducing the learning curve for implementation. Additionally, their compact design allows for easy integration into existing workflows without major facility modifications.
Key Features of Collaborative Robots
Advanced Safety Mechanisms
Safety forms the cornerstone of cobot technology, with multiple systems working together to ensure human protection. Force sensors throughout the robotic arms detect unexpected contact and trigger immediate stops or slowdowns. Many cobots also incorporate 3D cameras and proximity sensors to monitor their surroundings continuously. Power and force limiting technologies prevent injuries by restricting the robot’s strength based on safety parameters.
These sophisticated safety systems undergo rigorous testing to meet international standards for collaborative robots. Consequently, many cobots can operate without safety fencing, saving valuable floor space and integration costs.
User-Friendly Programming
Traditional industrial robots often require specialized programming knowledge and complex coding skills. Cobots, conversely, feature intuitive interfaces accessible to workers without robotics expertise. Hand-guidance programming allows operators to physically move the robot arm, demonstrating the desired movements. The cobot then records and repeats these movements with precision and consistency.
Graphical programming interfaces further simplify the process through drag-and-drop functionality and pre-built templates. This approach dramatically reduces setup times and enables quick task changes without extensive downtime.
Compact and Lightweight Design
The physical design of cobots prioritizes space efficiency and portability. Their small footprint allows integration into crowded production floors where space is premium. Many models can be mounted on mobile carts for deployment across multiple workstations as needed. Despite their compact size, modern cobots maintain impressive payload capacities suitable for numerous industrial applications.
Types of Collaborative Robots
Cobots come in four main categories based on their interaction methods with human workers:
- Power and Force Limiting Cobots: These most common models continuously monitor and restrict their force output to prevent injury during any contact.
- Safety Monitored Stop Cobots: These robots automatically stop all movement when humans enter their workspace and resume once the person leaves.
- Speed and Separation Monitoring Cobots: Using advanced sensors, these cobots adjust their speed based on human proximity, slowing down as workers approach.
- Hand Guiding Cobots: These allow direct human manipulation for teaching new tasks, combining intuitive programming with safe operation.
Applications of Cobots Across Industries
Manufacturing and Assembly
In manufacturing environments, cobots excel at repetitive tasks while maintaining consistent quality standards. They handle component insertion, fastening operations, and precise assembly tasks with remarkable accuracy. Many automotive manufacturers use cobots for installing small components like door handles and electrical parts. Electronics producers employ them for circuit board assembly and delicate component placement.
Cobots also shine in quality assurance roles, performing visual inspections with camera attachments. They can identify defects that might escape human attention due to fatigue or distraction.
Material Handling and Logistics
The physical demands of material handling make it an ideal application for collaborative robots. Cobots effortlessly move parts between workstations, reducing worker strain and injury risks. They load and unload machines, maintain consistent production flow, and perform repetitive lifting tasks. In warehouses, cobots assist with order picking, sorting, and inventory management functions.
Their flexibility allows quick reprogramming to handle different products as production needs change. This adaptability proves especially valuable in facilities with diverse product lines.
Packaging and Palletizing
Packaging operations benefit tremendously from cobot implementation. These versatile machines place products into containers, seal packages, and apply labels with precision. They arrange products in specific patterns for efficient shipping and storage arrangements. Palletizing cobots stack finished goods with consistent spacing and stability for transportation.
Food and beverage companies particularly value cobots for their ability to maintain hygiene standards while handling packaging tasks. Their gentle handling capabilities also make them suitable for fragile product packaging.
Welding and Finishing
Advanced cobots equipped with specialized end effectors perform welding tasks with remarkable consistency. They maintain perfect weld seams across complex geometries and challenging angles. Finishing applications include sanding, polishing, and painting operations requiring consistent pressure. These tasks, traditionally causing repetitive strain injuries, become safer through cobot assistance.
Healthcare Applications
In medical environments, cobots assist with patient handling, reducing strain on healthcare workers. They support surgeons through precise instrument positioning during complex procedures. Rehabilitation programs utilize cobots for consistent, personalized therapy exercises. Laboratory settings employ them for sample handling and repetitive testing procedures.
Leading Cobot Manufacturers and Their Innovations
Universal Robots (Denmark)
Universal Robots dominates the collaborative robot market with nearly half of global market share. Their product lineup includes the versatile CB3 series and advanced E-series models. Payload capacities range from 3kg to 16kg with reaches between 500mm and 1300mm. Their programming interface sets industry standards for user-friendliness and accessibility.
Techman Robot (Taiwan)
Techman Robot stands out through their integration of advanced vision systems directly into their cobots. Their TM series robots perform pattern recognition, barcode scanning, and object location without additional hardware. This unique capability makes them especially valuable in electronics manufacturing and quality control applications.
FANUC (Japan)
As a global automation leader, FANUC offers the robust CR and CRX cobot series. Known for reliability and durability, FANUC cobots handle demanding industrial environments with ease. Their precision makes them particularly popular in automotive manufacturing and machine tending roles.
ABB Robotics (Switzerland)
ABB’s YuMi cobot features an innovative dual-arm design perfect for intricate assembly tasks. The anthropomorphic configuration allows YuMi to handle complex operations requiring coordination between multiple manipulators. Their safety systems enable true side-by-side work with human operators.
Other Notable Manufacturers
The cobot ecosystem includes numerous other innovative companies, each with unique strengths:
- KUKA (Germany): Produces the precision-engineered LBR iiwa series for sensitive applications
- Doosan Robotics (South Korea): Offers versatile models with multiple arm lengths and payloads
- AUBO Robotics (China): Focuses on lightweight, affordable cobots for smaller businesses
- Rethink Robotics (Germany): Creates human-centric designs with advanced AI capabilities
- Yaskawa Motoman (Japan): Manufactures robust cobots for demanding industrial environments
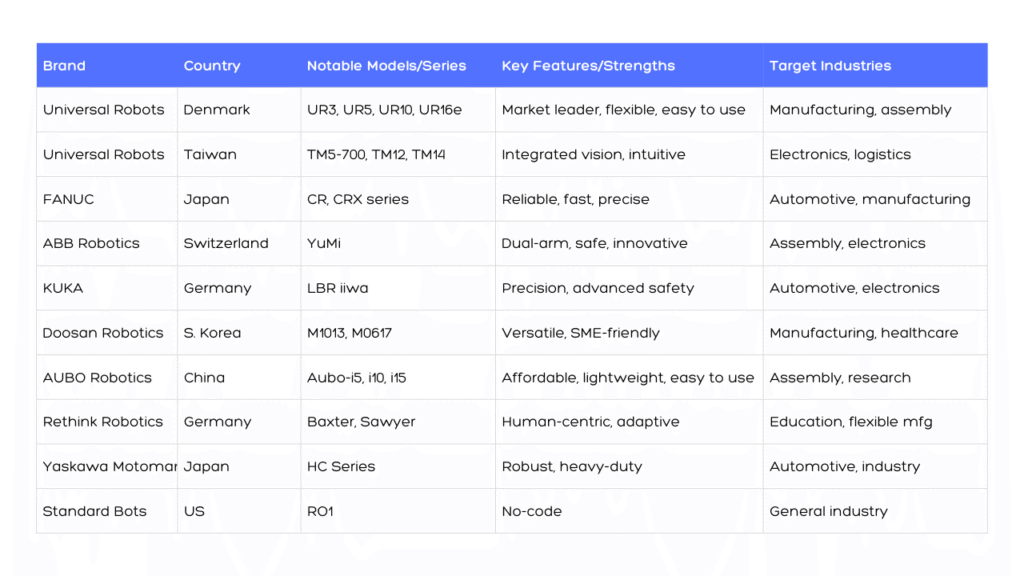
Benefits of Implementing Cobots
Enhanced Workplace Safety
By taking over hazardous tasks, cobots significantly reduce workplace injury risks. Their built-in safety features prevent accidents during collaborative operations. Workers experience less physical strain from repetitive motions and heavy lifting. This improved safety translates to fewer lost workdays and compensation claims.
Many companies report dramatic decreases in ergonomic injuries after cobot implementation. The reduction in physical strain often leads to improved employee morale and job satisfaction.
Increased Productivity and Quality
Cobots maintain consistent performance without fatigue or distraction factors. They execute repetitive tasks with perfect precision, reducing error rates and material waste. Human workers freed from monotonous tasks can focus on complex problems requiring creativity. This collaboration between human ingenuity and robotic precision creates optimal production environments.
Quality improvements typically manifest immediately after cobot deployment. Many manufacturers report defect reductions exceeding 30% in processes handled by cobots.
Cost Efficiency and ROI
Compared to traditional industrial robots, cobots offer more affordable initial investments. Their simple programming reduces implementation costs and ongoing maintenance expenses. Many businesses achieve complete return on investment within 12-36 months. Small batch production becomes economically viable through quick changeovers between tasks.
Flexibility and Scalability
Cobots adapt quickly to changing production requirements through simple reprogramming. They can be redeployed to different workstations as production needs shift. Their modularity allows gradual expansion of automation capabilities. This flexibility proves especially valuable for manufacturers with seasonal demand fluctuations.
Challenges and Considerations for Cobot Implementation
Technical Limitations
Despite their versatility, cobots have certain limitations compared to traditional industrial robots. Their payload capacities typically max out around 16kg, restricting some heavy-duty applications. Operating speeds remain limited due to safety considerations when working alongside humans. Some complex tasks still require specialized end effectors or additional sensing capabilities.
Integration Challenges
Integrating cobots into existing production systems sometimes presents technical hurdles. Legacy equipment may require interface modifications to communicate with cobots effectively. Workflow optimization often demands rethinking established processes for human-robot collaboration. IT infrastructure might need updates to support data collection from cobot operations.
Human Factors and Change Management
Employee acceptance represents a critical factor in successful cobot implementation. Workers may initially express concerns about job security or changing responsibilities. Proper training programs help employees transition to working alongside robotic colleagues. Management must communicate clear visions for human-robot collaboration.
Organizations that emphasize cobots as tools to enhance human capabilities rather than replacements typically experience smoother transitions. Involving workers in implementation planning often increases acceptance rates dramatically.
Future Trends in Collaborative Robotics
AI and Machine Learning Integration
The next generation of cobots incorporates increasingly sophisticated artificial intelligence capabilities. Machine learning algorithms enable cobots to improve performance through experience. Computer vision systems become more advanced in recognizing objects and environmental changes. These enhancements allow cobots to handle greater variability and complexity in tasks.
Mobility and Flexibility
Autonomous mobile platforms are merging with collaborative robot arms for increased versatility. These mobile cobots navigate workspaces independently, providing assistance where needed most. The ability to change locations without human intervention dramatically expands potential applications. Industries from healthcare to retail benefit from this enhanced mobility.
Enhanced Human-Robot Interfaces
Natural language processing enables more intuitive communication with collaborative robots. Gesture recognition systems allow workers to direct cobots through simple movements. Augmented reality interfaces provide visual guidance for programming and troubleshooting. These advancements reduce training requirements and improve operational efficiency.
Industry 4.0 Integration
Cobots increasingly connect to broader manufacturing execution systems for coordinated operations. Data collection capabilities provide valuable insights for continuous improvement initiatives. Real-time monitoring allows predictive maintenance to prevent downtime. This connectivity transforms cobots from standalone tools into integral components of smart factories.
Getting Started with Cobots: Implementation Guide
Assessing Needs and Opportunities
Before selecting a cobot system, thoroughly analyze current workflows for automation potential. Identify repetitive, ergonomically challenging, or precision-critical tasks as prime candidates. Consider available space, existing equipment compatibility, and required payload capacities. Calculate potential ROI based on productivity gains and labor reallocation possibilities.
Selecting the Right Cobot System
Consider payload requirements and reach specifications for intended applications. Evaluate programming interfaces against your team’s technical capabilities. Assess safety features relative to your specific collaborative requirements. Research vendor support options and training resources thoroughly.
Many manufacturers offer trial periods or simulation software for testing before purchase. These opportunities provide valuable insights into real-world performance capabilities.
Training and Deployment
Develop comprehensive training programs for operators, programmers, and maintenance staff. Start with simple applications to build confidence and experience. Gradually expand complexity as team members gain proficiency with the system. Document standard operating procedures for consistent implementation.
Measuring Success and Continuous Improvement
Establish clear metrics for evaluating cobot implementation success. Track productivity improvements, quality metrics, and employee satisfaction indicators. Analyze data from connected cobots to identify further optimization opportunities. Create regular review cycles for assessing and enhancing cobot applications.
Conclusion: The Collaborative Future of Work
Cobots represent more than just another automation technology; they embody a fundamental shift in human-machine interaction. Rather than replacing workers, they enhance human capabilities through effective collaboration. This partnership leverages the unique strengths of both humans and robots for optimal outcomes.
As cobots continue evolving, they will transform more industries and applications. Their increasing intelligence, flexibility, and ease of use will make automation accessible to businesses of all sizes. Forward-thinking organizations already embrace this collaborative approach to gain competitive advantages.
The future workplace will likely feature humans and cobots working together seamlessly across various industries. This evolution promises enhanced productivity, improved safety, and more engaging work experiences. By understanding cobot capabilities and implementation strategies today, businesses position themselves for success in this collaborative future.
To find the best cobots for your work and to save hundreds, head to robotbids.